Equip yourself with the bulk bag unloader customization guide, your essential roadmap for navigating the dynamic world of bulk bag handling and unloading. Optimize your unloading process and join us as we delve into the art of customization, helping you tailor your bulk bag unloader to meet the exact needs of your specific operation.
Why Do You Need a Bulk Bag Unloader Customization Guide?
If you’re in the market to upgrade or extend your bulk bag unloading line, you must consider that not all bulk bag dischargers are created equal. That’s why it’s essential to have a step-by-step guide to selecting bulk bag unloader components.
After all, the guide ensures that you make informed decisions and select tailored solutions that not only meet but exceed your requirements. With the right customization guide, you can achieve efficiency, safety, and precision in your bulk bag handling operations, all while saving time and resources.
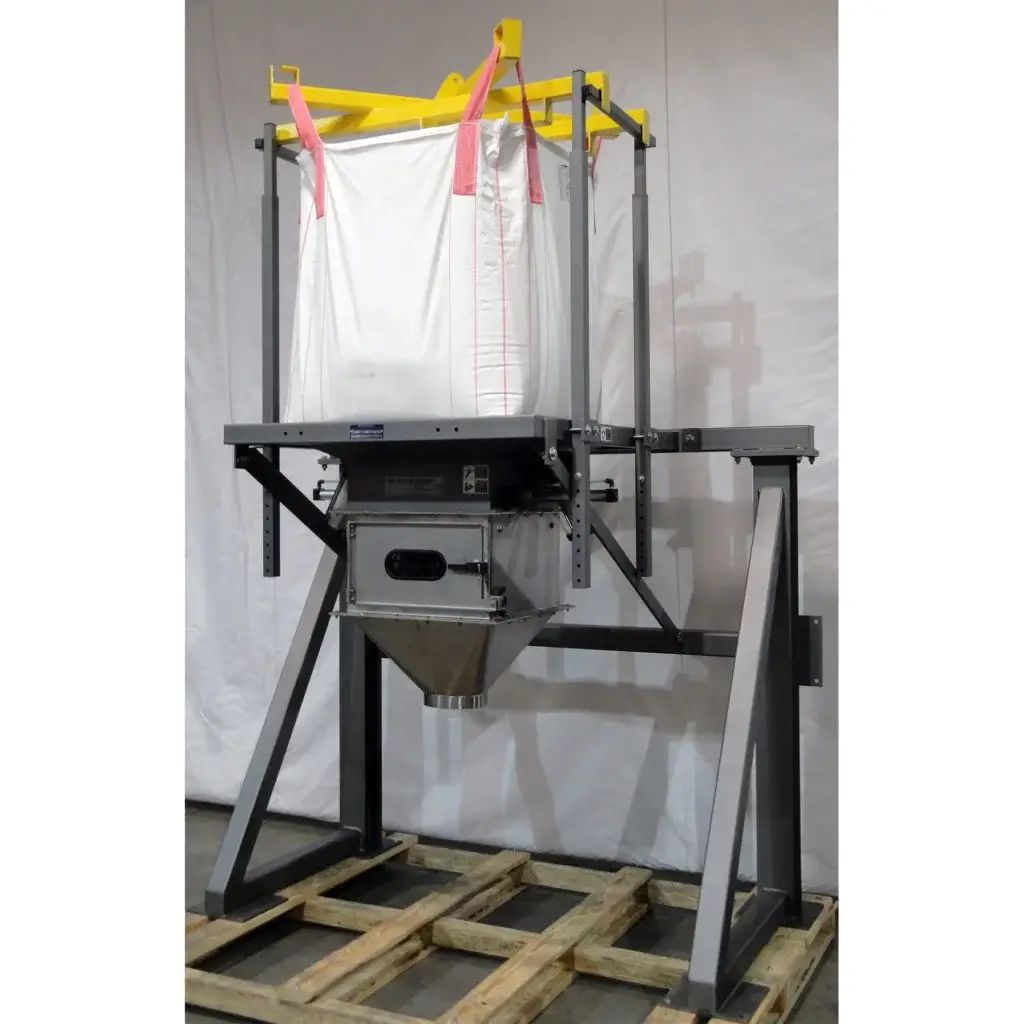
Get All the Needed Help When Selecting Bulk Bag Unloading Equipment
Spiroflow, a trusted name among belt conveyor manufacturers, stands at the forefront of innovation in the bulk bag unloading market. Our diverse array of options and customizations are designed to meet your unique needs. Whether you’re contemplating the simplicity of standalone frame designs or the sophistication of semi-automated unloading systems complete with densifying vibration tables, our guide helps you navigate these choices. Discover how Spiroflow empowers you to customize your bulk bagging system, aligning it seamlessly with a wide range of budget constraints and discharge requirements.
Define Bulk Bag Unloading Requirements
Before delving into the specifics of bulk bag unloader customization and conveyor technologies, it’s crucial to begin by evaluating your material, process needs, and bag requirements. These fundamental considerations lay the foundation for a safe and dependable discharging solution.
Proceed with other important considerations to ensure you end up with a safe and reliable discharging solution, including:
- Material properties and flow characteristics,
- Size and type of bags that will be handled,
- How the bags will be handled,
- Fork truck or hoist,
- Headroom/space constraints,
- Weighing/batching requirements,
- Downstream process requirements,
- Bag removal and disposal,
- Dust containment hygienic requirements.
Step 1: Understand The Material Characteristics
When it comes to designing a bulk bag unloader that seamlessly integrates with conveyor belt systems, understanding material characteristics is paramount. These characteristics play a pivotal role in tailoring your solution to meet your unique needs. The range of considerations is extensive, with some of the most critical factors including:
- Material Type – Dust Containment
Some materials pose health and environmental risks, making dust containment and operator protection crucial. To address these concerns, seals can be added between the bulk bag and discharger to prevent dust escape.
Options include rubber membrane seals at the base, double dust seals for dusty single-trip bags, and “Glove Box” unit chambers for complete containment. Additionally, a hygienic spout connection can enhance sealing between the bulk bag and downstream processes. Integrating dust collectors into the discharger frame allows dust to be reclaimed downstream, reducing product loss.
- Explosion Proof/Hazardous Options
In situations where you are dealing with the discharge of combustible materials or working within explosion-prone areas, it is essential to take extra precautions to safeguard both personnel and equipment.
This involves the utilization of specialized discharge systems designed for such conditions. These tailored options are adaptable to various area classifications and incorporate key safety features like explosion-proof motors, pneumatic vibrators, intrinsically safe sensors, as well as static grounding and monitoring systems.
- Material Flow Characteristics
Flowability will determine if flow aids are required and their type. Various designs are available, ranging from different types of paddles or massagers to vibration, mechanical agitators or air “pads” and “sweep” systems.
Some materials will agglomerate in a bulk bag to the extent that they will still not discharge using typical flow aids. In these cases, a bulk bag conditioner may be required to break the set of materials and reduce the size of large lumps, thereby allowing a bulk bag discharger to empty the bag. These units can be of a standalone design or can also be incorporated into some discharger designs.
Step 2: Know Your Bag Specifications
If you’re a high-volume consumer of raw materials using FIBCs and have influence over the bag specifications, you can collaborate with conveyor systems manufacturers to align your needs. However, if your supplier provides specific bag styles, it’s essential to grasp key parameters.
- Dimensions
Determine if the base dimensions are within the typical range of 35″ x 35″ to 41″ x 41″. If the dimensions are outside of this range, a smaller or larger bag support (dish) and a larger frame may also be required. In addition to the base dimensions, the range of side seam heights of the bags to be handled also needs to be known, as this will determine the height of the discharger structure and whether space-saving options need to be considered.
- Lifting Loops
There are two main styles of lifting loops, lay flat and cross corner, and both are normally compatible with standard bag lifting frames, but the details should always be confirmed to ensure a safe and reliable fit and if any customization is required.
- Liner/Sealing Requirements
Determine if the bags that will be used will incorporate a liner to prevent the ingress of foreign materials or moisture into the bulk bag or the egress of very fine powders through the fine stitching and weaving of the bulk bag.
The two primary types of liners used in FIBCs are “From-fit” and “Loose Tubular.” If the bag has a loose tubular liner, there are different types of “liner tensioners” that can be used to either hold the liner in place as the bag discharges or partially wind up the liner as material flows out of it to prevent the liner from exiting with the material and becoming entangled in downstream equipment.
- Base Construction
It’s important to note that not all Flexible Intermediate Bulk Containers (FIBCs) come equipped with a discharge spout. Consequently, having a clear understanding of the base construction of the bags you intend to handle becomes pivotal in the discharger’s design process.
If the bag features an outlet spout, it becomes crucial to ascertain specific details such as the diameter and length of the spout. These particulars play a vital role in ensuring the precise functioning of elements like spout closure bars and hygienic spout connections.
- Flat Bottom
Known as single trip bags, these bag varieties necessitate a custom-designed knife for cutting their base as they are lowered into the discharger. It’s essential to emphasize that operator safety is paramount, and this design ensures that there’s no need for operators to reach beneath a suspended load to carry out this task.
- Conical Bottom
Usually, a standard discharger can be used with this type of bag, but care must be taken to ensure that the ties that secure the cone during shipping can be safely released once the bag is lowered into the discharger.
Step 3: Bulk Bag Handling Requirements
Check whether the bag will be introduced into the discharger through a forklift or if a motorized hoist and trolley will be employed for loading. This choice significantly impacts the discharger frame needed, ensuring optimal integration with conveyor solutions.
Assessing Filled Bag Weight and Equipment Capacity
The filled weight of the bulk bags must be assessed to confirm the bulk bag discharger frame design will safely handle the upper limit. It will also define the capacity of the hoist and trolley required if a monorail-style discharger is being considered.
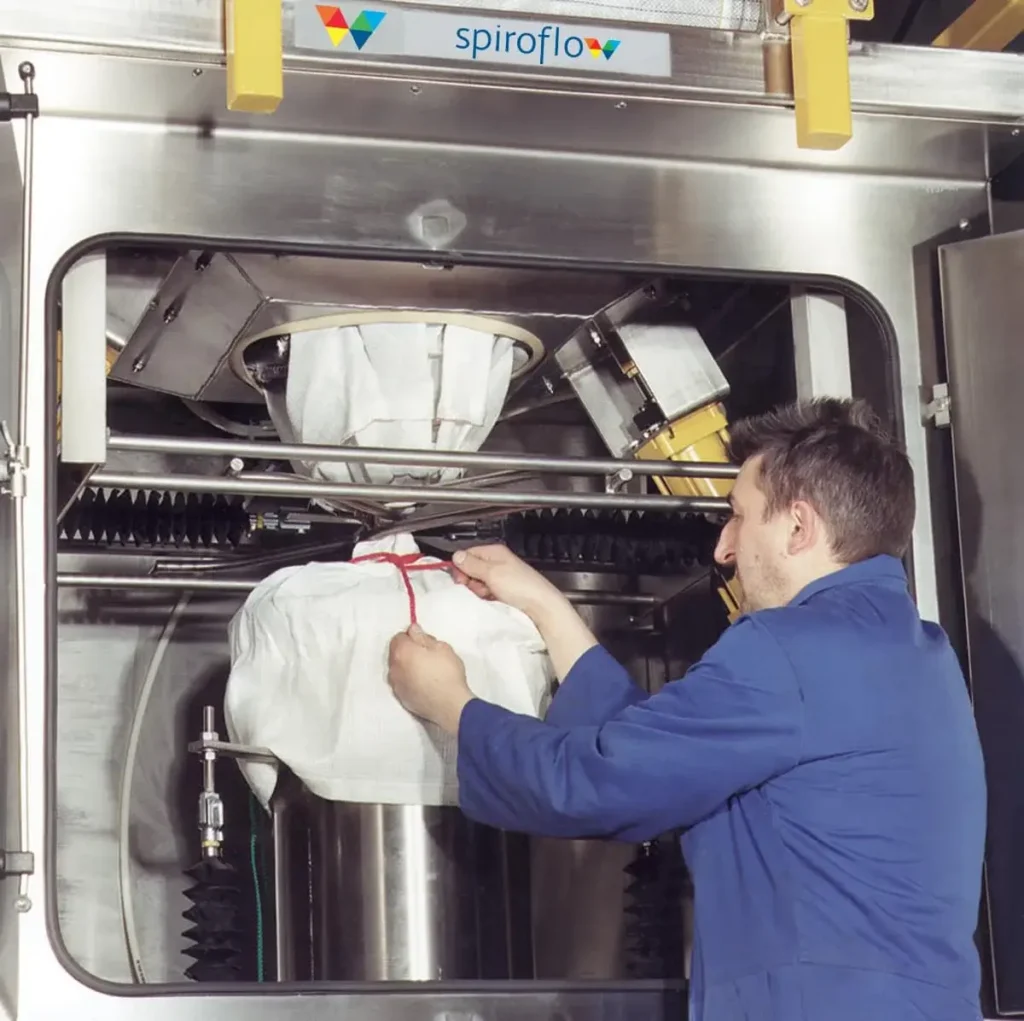
Step 4: Determine the Method of Downstream Material Transfer
When addressing material discharge from the bag, two primary methods come into focus: gravity feed and conveyor feed systems. In a gravity feed, material freely descends from the bulk bag discharger into the designated vessel or container.
Alternatively, in a conveyor feed system, material is efficiently transported through a mechanical or pneumatic conveyor system. It’s important to note that not all conveyors are suitable for direct flood feeding from the discharger. Therefore, thoughtful design considerations are necessary to accommodate a metering device like a rotary airlock valve or similar mechanism between the discharger and the belt conveyor system.
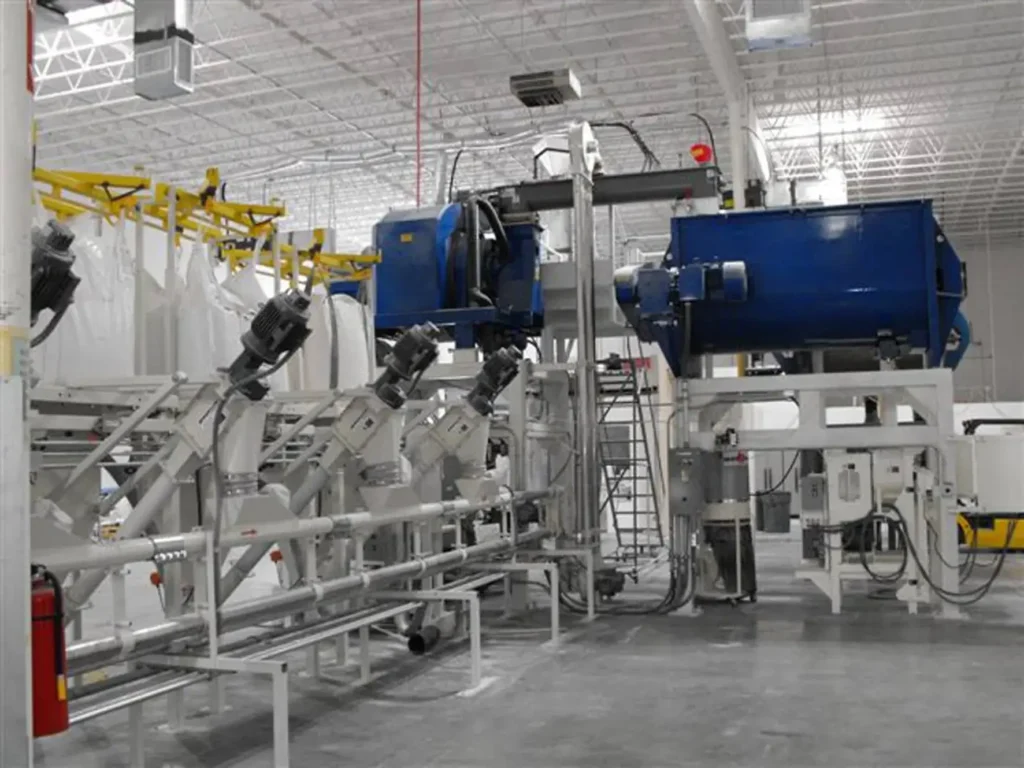
Step 5: Define Weight Batching or Dosing Requirements
The next crucial phase is defining weight batching or design requirements for your bulk bag unloading process. Metering the material from a bulk bag to provide an accurately weighed amount of material is often a requirement. This can be done in two ways: loss-in-weight (LIW) or gain-in-weight (GIW).
Loss-in-weight (LIW) requires that the discharger or a portion of the discharger, along with the metering/feeding device, are weighed, and a control system is used to monitor the loss in weight of the system as material is fed to the next step in the process.
Gain-in-weight (GIW) is used when the vessel or container that is being fed by the bulk bag system is on load cells. The control system monitors the gain-in-weight of the weighted vessel to control the feed device.
Process Integration
Volumetric-type feed devices such as a flexible screw conveyor, airlock, and cable conveyor can be used to move material from the bulk bag discharger to the next stage of the process. Almost any type of conveyor belt system can be integrated with a bulk bag discharger.
Step 6: Customize the Bulk Bag Unloading Station
Many additional options can be added to a bulk bag discharger design. Here are some of them:
- Mobile Options
For manufacturers who need to move their unloaders to different locations, this discharger can be locked in place while in use and then wheeled to another location in the plant easily.
- Hygienic Requirements
It’s also important to understand any hygienic requirements, including the cleaning process of the discharger. Additional options can be added to the bulk bag unloader, such as spray balls and drain ports, in order to facilitate cleaning in place. Also, surface finishes, frame design, and materials of construction can all be specified to meet additional hygienic requirements.
- Dish Cover Assembly
In order to prevent foreign material from entering the discharger and possibly contaminating the internal parts that come in contact with the material, a pneumatically operated cover can be used to seal the bulk bag discharger dish/tray/hopper when not in use.
- Integral Bag Dump Station
For small (typically 50 lb) bags that also need to be emptied into a bulk bag discharger, a second bag dump enclosure with a safety grid can be incorporated under the standard untie chamber, or an oversized untie chamber incorporating these features can be added.
- Operator Safety Considerations
The design of the discharger must allow the operator to easily and safely untie/retie an outlet spouted bag, so dusting (see above) is often a critical safety consideration. Additionally, removing a partially emptied bulk bag from the discharger is often a requirement.
In order to accomplish this task, a device must be included in the discharger design to close off the outlet spout so that it can be retied, allowing the partially emptied bag to be removed. It is clearly imperative that any such devices are safely interlocked to avoid inadvertent operation when the operator is working on a bag spout.
- Bag Removal and Disposal
The potential for dusting must also be considered when removing the bag from the discharger. Every dry bulk material should be assessed for its risks and tendency to create dust. There are different methods of evacuating the dust-laden air that remains in an empty bulk bag before removal, and dust-free bag compacting and sealing stations can be added as required in these circumstances.
Step 7: Testing Your Selected Design
Following the steps above will help you to determine the right style or design of bulk bag discharger for your specific process needs and what customizable options you should consider in order to maximize the safety and efficiency of your system. Furthermore, these steps highlight the importance of considering customizable options that enhance both safety and efficiency, including the integration of conveyor belts.
The final step in the process is to work with a reputable manufacturer who offers a broad range of designs and options that will meet your needs and who has the ability to test the recommended solution in order to confirm the most appropriate design has been reached.
Some examples of typical discharger designs available from Spiroflow Systems include the following:
- Simple Support Frame
Simple support frames are suitable for applications in which the product is discharged without the need for flow aids, is dust-free, does not need regulation of the flow of materials at any point in the process, and has continuous operator supervision in place.
- Discharge by Volume
This universal type of bulk bag unloader provides controllable discharge rates by volume and is typically used for applications with poor-flowing materials.
- Discharge by Weight
Loss-in-weight bulk bag unloaders offer total control over the amount of product that is successfully dispensed from the bag and can be varied for individually selected batch amounts or fully integrated with process controls for continuous batch production.
This loss-in-weight model has a specialized batch controller that offers both bulk and trickle feed options for optimal dispensing of materials. It also has a “Pause-Resume” feature that automatically pauses the discharging operation when a bulk bag is found to be empty and retains in memory the amount that has been dispensed.
- Discharge With Height Restrictions
Low Loader models, incorporating a split upper and lower frame, are ideal for areas in which there is restricted headroom that typically causes issues for bag handling operations. By pairing this type of bulk bag discharger with a suitable conveyor system, ingredients can be fed from the bag by volume or by weight and can be moved into other mixing or processing equipment proportionately.
In addition to handling bulk bags, the height of the access door can be designed to receive small bags as well (typically around 50 lbs or less), which is beneficial to processors who continue to receive minor ingredients in smaller bags. Processors with batching operations can also choose to have several upper frames in use with one discharge station in order to significantly speed up bag change over time.
- Discharge Without the Use of Forklift Assistance
An Integral Hoist model offers a fully self-contained environment for dust-free and controllable bulk bag emptying. This piece of equipment has an integral “I” beam and hoist that loads bags into the discharger, saving space and the need for forklift assistance.
- Discharge of Rigid Bins, Octabins, or Sacks/Bulk Bags
This multi-container discharger model is a versatile option that allows processors to discharge materials from a variety of container types, such as rigid IBCs, octabins, and bulk bags and sacks. It is suitable for batching operations that require multiple ingredients from several different sources or methods of supply.
- Discharge Single Trip Bags
Single-trip bulk bags are commonly used within plant environments that process low-value or hazardous materials and, therefore, require a dust-free and controllable emptying method.
These disposable bags have no bottom spout and require a static or pneumatic knife to open the bag during the unloading process.
- Discharge for High Containment Applications
For high-containment bulk bag discharging applications such as pharmaceutical discharging, there are options that are specifically created with hygienic design, dust-containment, and cross-contamination considerations in mind. These FIBC dischargers are often used in dairy and pharmaceutical applications, where spillage and contamination should be avoided at all costs.
Unlock Your Customized Bulk Bag Unloading Success Today
Discover the pathway to unlocking the full potential of your bulk bag unloading operations. Find a comprehensive guide that offers the knowledge and insight you need to elevate your system to new levels of efficiency and precision.
Whether you are in search of advanced conveyor belt solutions or state-of-the-art industrial conveyor systems, Spiroflow is the unrivaled leader in bulk bag handling solutions. Choose your dedicated partner throughout this transformative journey. Take the first step by contacting us today to begin the customization process and start your system’s journey toward unparalleled success.