Choosing between different mechanical conveyor choices for your specific needs is essential for operational success and cost-effectiveness. At Spiroflow, we offer an extensive selection of conveyors to suit various processing requirements. Our main goal is to deliver a safe, efficient, and dependable conveying solution tailored to your specific application.
We collaborate closely with our clients to ensure they receive the perfect conveyor system that meets their unique requirements. With years of experience in this field, we are committed to providing this service to you. This article aims to guide you through key considerations when choosing a conveyor manufacturer. Additionally, it includes a useful comparison chart showing a high-level overview of different conveyor performances across various metrics.
Mechanical Conveyor Choices
When selecting a mechanical conveyor, several critical factors must be considered to ensure the chosen conveyor belt systems align with your operational needs and long-term objectives. The right conveyor choice hinges on a thorough understanding of your material handling needs, operational integration, maintenance expectations, and long-term energy considerations. These factors collectively ensure that your conveyor system not only meets immediate requirements but also supports efficient, sustainable, and cost-effective operations in the long run.
Consider Product Attributes
The nature of the product you intend to convey plays a crucial role in deciding the appropriate conveyor system. It’s important to consider the specific properties of your material. Engineers will require information about the material’s bulk density, particle size, moisture content, temperature, and level of abrasiveness. Additionally, consider whether the product is hygroscopic or prone to segregation. You should also evaluate if the product is cohesive and if any other unique properties may influence its conveyability.
Required Performance and Function
The next thing you should evaluate when choosing a conveyor is the required performance and function. Consider the following aspects when choosing a conveyor system:
- Determine the required speed and volume of material that needs to be conveyed.
- Assess the available space and any layout restrictions that might impact the conveyor’s design.
- Decide on the type of materials necessary for the construction of the conveyor to ensure durability and compatibility with the product being conveyed.
- Evaluate if your operation requires the conveyor to have more than one entry or exit point for materials.
- Determine if the material needs to be elevated or moved across various levels.
- Consider if the operation requires the conveyor to have an adjustable conveying rate.
- Plan how the material will be introduced into the conveyor system.
- Ascertain if the product requires delicate handling to prevent damage.
- Decide if the conveyor needs to be enclosed to manage dust, prevent contamination, or for safety purposes.
- Evaluate the necessity of integrating a dust collection system with the conveyor.
- Consider if there is a need to measure the weight of ingredients being delivered by the conveyor.
These considerations are essential to ensure that the selected conveyor system meets all operational requirements and is tailored to your specific needs.
Operating Features
When selecting a conveyor, it’s important to ensure that it can accommodate the specific conveying distance required for your operation. Additionally, the conveyor should be capable of handling both your current and future volume needs. Consider the financial aspects, such as the initial installation costs and the ongoing operating expenses, to assess its economic feasibility. It’s also crucial to determine whether the conveyor can be seamlessly integrated into your existing setup.
If your operations demand a sanitary environment, the conveyor must be suitable for such conditions. For operations involving bag or sack handling, a conveyor with an integrated dump hopper could be essential. If mobility is a key factor, a mobile conveyor might be necessary. Lastly, in environments where safety is a concern, particularly regarding explosive materials, selecting an explosion-proof conveyor is vital.
Service Life
Consider the expected operational lifespan for which the conveyor will be used. There are conveyors designed for light-duty tasks, ideal for sporadic or short-term use, and others that are built for heavy-duty purposes, aimed at sustained, long-term operation. It’s important to evaluate the required service life of the conveyor to guarantee it’s capable of meeting the demands of your specific application.
Long-Term Energy Requirements
Take into account the long-term implications of the conveyor’s energy usage on its operating costs. It’s important to assess not just the immediate energy requirements but also how these will translate into ongoing expenses. Energy-efficient conveyors, while potentially more costly upfront, can offer significant savings over time, reducing the overall cost of operation.
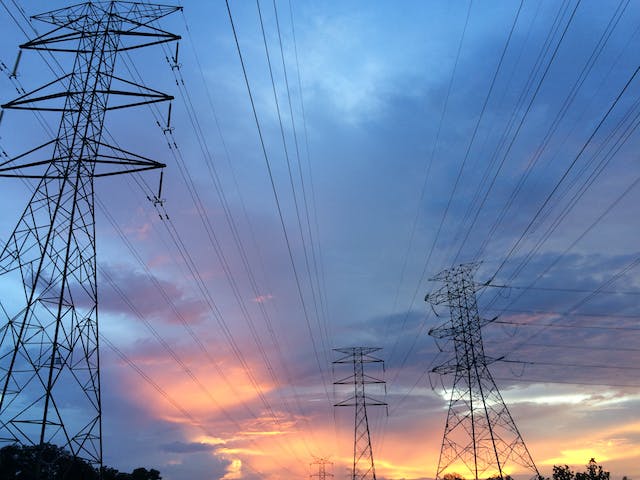
Choose Between Different Conveyor Systems Manufacturers
We advise partnering with a supplier who provides a diverse range of conveyor options when choosing a belt conveyor system. A supplier with a broad selection is likely to have the expertise needed to meet your specific conveying requirements and to guarantee that the chosen conveyor will endure the operational intensity for the entire lifespan of the process. Such a supplier is well-equipped to offer guidance on which conveyor model is most suitable for handling your material while also ensuring an optimal balance of affordability, low operational costs, and high efficiency.
Testing the Material
Ideally, the supplier should possess a test laboratory equipped with various types of conveyor technologies. This facility enables you to ascertain which conveyor belt system is most adept at handling your specific material and operating conditions. Additionally, it’s beneficial to request references from the supplier. By contacting previous customers who had similar applications, you can gauge their satisfaction with the conveyors they purchased and get insights into the supplier’s reliability and the performance of their conveyors in real-world conditions.
Performance Guarantee
In conclusion, it’s essential to ensure that your chosen supplier offers guarantees regarding the conveyor’s ability to effectively transfer your material and operate reliably and economically over time. Spiroflow stands behind all equipment solutions that have been thoroughly tested in our test lab, assuring their performance and long-term efficiency. This commitment to quality and reliability is a key aspect of our service, ensuring that our customers receive dependable and cost-effective conveyor solutions.
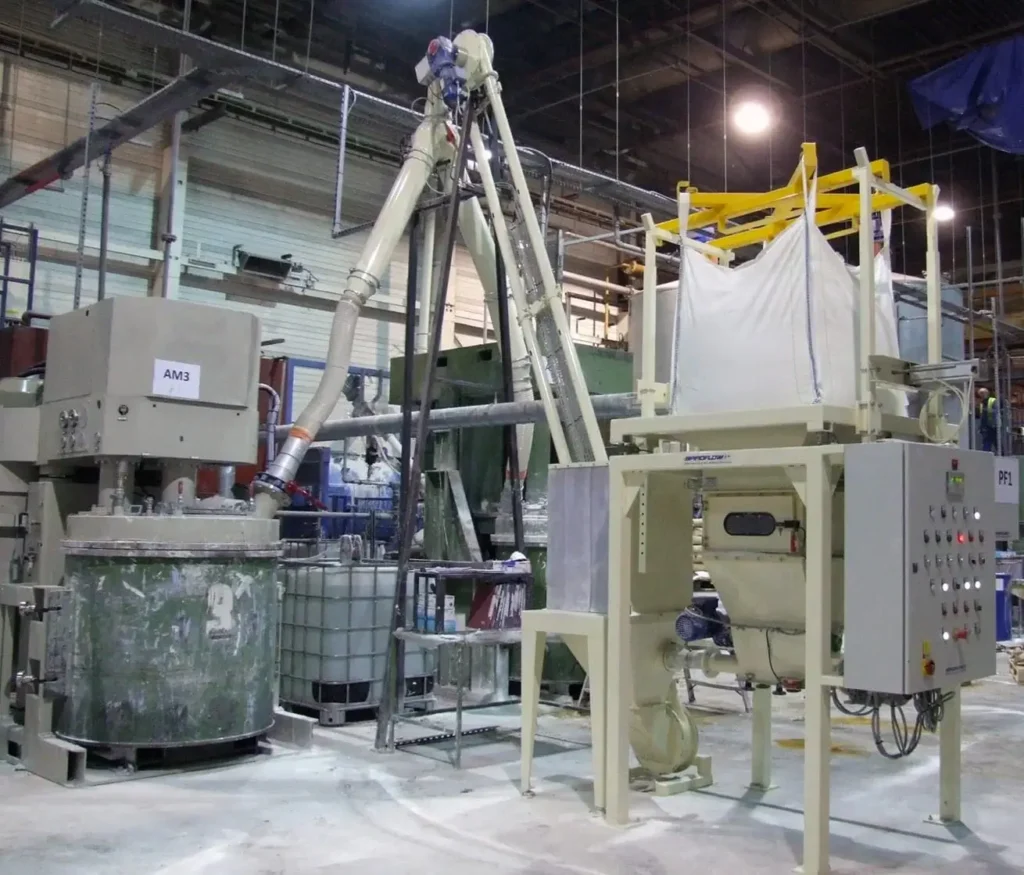
Explore the Comparison for Mechanical Conveyors
The comparison illustrates the differences between the following:
- Flexible screw conveyors,
- Aero mechanical conveyors,
- Tubular drag conveyors,
- And pneumatic conveyors.
Flexible Screw Conveyors
Often known by various names, these conveyors are commonly called screw augers, flexible augers, flex conveyors, auger screws, flexible spiral conveyors, helical or helix conveyors, or spiral screw conveyors. Characterized by its dust-free operation, a flexible screw conveyor is energy-efficient, requires low maintenance, and is cost-effective. These conveyors are known for their gentle handling of materials and consistent remixing capabilities. Additionally, they are straightforward to install.
Aero Mechanical Conveyors
Aero mechanical conveyors are designed for high-capacity conveying and complete batch transfer. They operate using a cable and disc assembly, which moves through a fully enclosed tubular system. This system fluidizes materials at high speeds along a circuit. Known for their efficiency, aero mechanical conveyors are a dependable choice for moving materials between processes, and they do so with relatively low energy consumption.
Tubular Drag Conveyors
Tubular drag conveyors work using either a cable and disc assembly or a chain and disc assembly. Constructed from a series of both straight and curved tubes or structural pipes, they create a completely enclosed system. This system gently moves material along the conveying path between the discs. These conveyors are capable of handling complex circuits, including multiple inlets and outlets, and are effective for total batch transfers. However, their conveying rate is typically slower compared to flexible screw or aero mechanical conveyors due to a lower operating speed. The speed of operation in drag conveyor belts is influenced by the configuration of the circuit and the distance the material travels.
Contact the Best Conveyor Manufacturers if You Still Have Questions
With over 45 years of experience in the bulk material handling industry, we are well-equipped to assist you in finding the ideal conveyor belt solutions for your process. Don’t hesitate to reach out to us with your queries about industrial conveyor systems. We’re committed to working alongside you to ensure you choose the right conveyor that meets all your process needs. Contact us today to start the conversation and take the next step toward optimizing your material handling operations!