In a remarkable feat of engineering and collaboration, Spiroflow helps a customer out of a sticky situation. This text highlights how Spiroflow Systems Inc. provided an innovative solution to Jowat Adhesives Inc., a prominent adhesive manufacturer in High Point, North Carolina. Seeking to enhance their manufacturing plant’s efficiency and environmental safety, Jowat Adhesives turned to Spiroflow for a custom-designed bulk bag discharger/sack tip station.
Spiroflow Helps a Customer Out of a Sticky Situation With an Excellent Bulk Bag Discharger/Sack Tip Station
Spiroflow was the choice of Jowat Adhesives Inc. when it came to purchase a completely enclosed dust-tight bulk bag discharger/sack tip station for its manufacturing plant in High Point, North Carolina, USA. The plant produces a comprehensive range of adhesives for a variety of industries.
“We wanted to avoid any dust contamination from the many different resin flakes running through the discharger used to produce our broad line of industrial adhesives,” says Mike Kuhn, Plant Engineer at Jowat Adhesives, Inc. “We were seeking a system that was totally enclosed and didn’t have seams or small holes, like some other dischargers, through which dust could penetrate and contaminate the working environment.”
We Created Custom-Made Conveyor Solutions to Meet the Needs of Jowat Adhesives Production Process
To find a discharger that met their requirements, which included the facility to handle 50 lb bags, Kuhn and some of his fellow engineers visited a powder show in Charlotte, North Carolina, back in March 2008. At the Spiroflow Systems Inc. stand, they found exactly what they needed in the Spiroflow Type 2 bulk bag discharger.
We custom-designed our discharger to meet Jowat Adhesives’ exact specifications. Not only does the unit accept two sizes of bulk bags, but it incorporates a bag tip station too. Within two months, the unit was installed at the plant in High Point and, according to Kuhn, has been running 24/7 and operating flawlessly ever since.
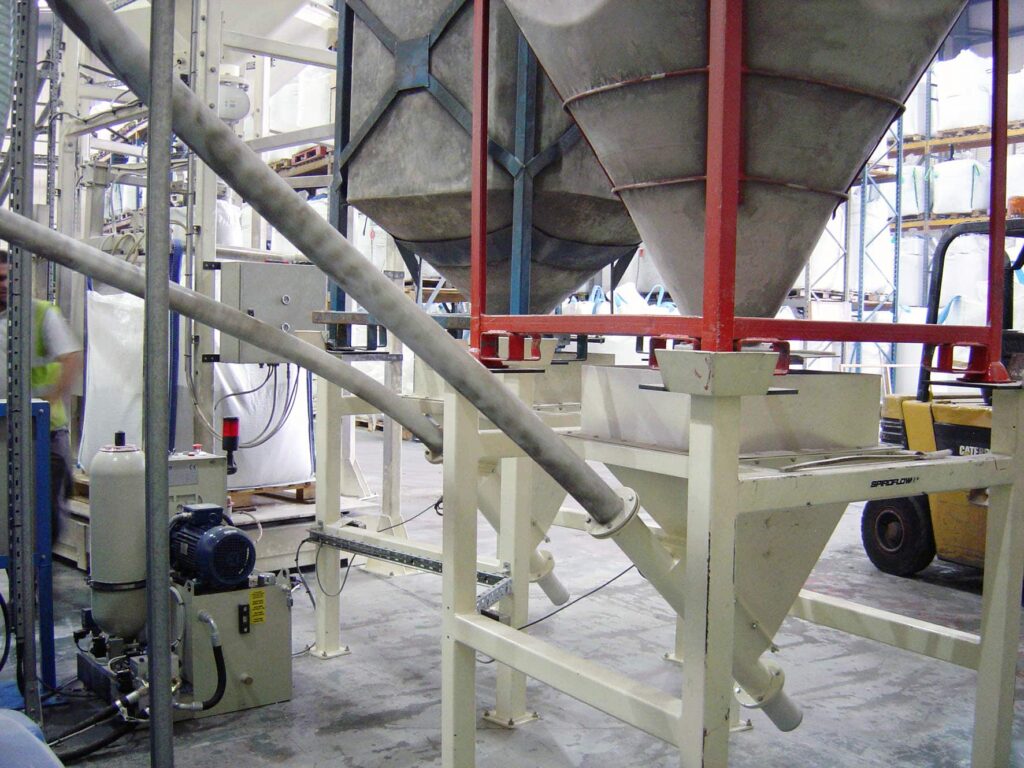
The Company Was More Than Satisfied With Their New Unit
“The Spiroflow discharger is clean, operator-friendly, easy to load, compact, and takes up less space than the other dischargers in our plant,” Kuhn advises. “Our productivity and environmental quality have also been enhanced,” Kuhn adds. To remove any dust that escapes from the bag during untying or removal, the discharger’s dust containment cabinet connects to Jowat’s central dust collection system.
How Have Our Industrial Conveyor Systems Been Working for Jowat Adhesives?
The Spiroflow Type 2 bulk bag discharger at Jowat Adhesives has a surge hopper that was custom-designed in stainless steel to accept resin flakes from 1,000 lb Supersacks, 500 lb Mini-Sacks or 50 lb bags. Resins are gravity-fed from the discharger, through the surge hopper, and into a vacuum conveyor at the base of the discharger.
The vacuum conveyor transfers the resins from the discharger to a process vessel in a controlled and dust-free manner. “The manual dumping station facilitates the addition of minor additives into the process and gives Jowat a fall-back position should the supply of material in the larger bulk bags be disrupted,” notes Mathias Lee, Vice-President of Sales at Spiroflow Systems Inc.
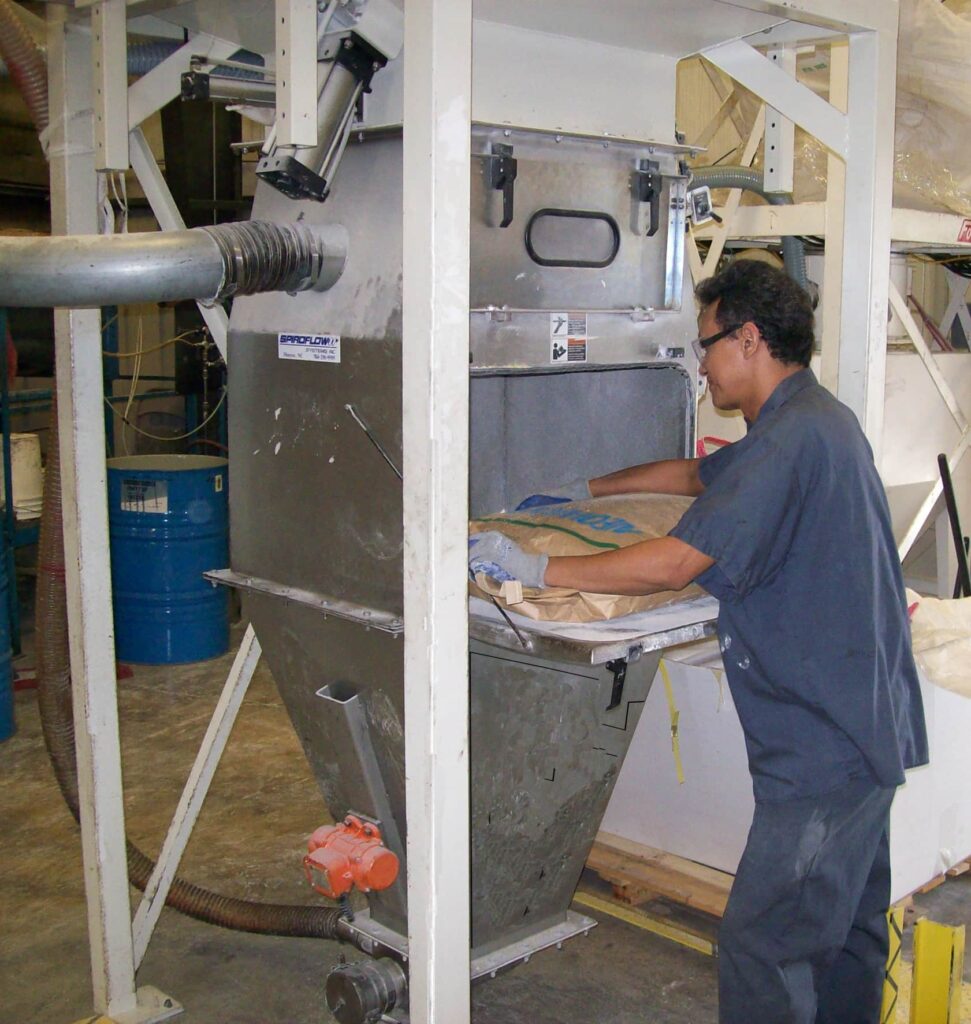
The Spiroflow Type 2 Bulk Bag Discharger in Detail
The Spiroflow Type 2 bulk bag discharger at Jowat Adhesives includes spring-loaded arms to support the bag lifting frame, the integral bag dumping station, bag spout closure bars, and a bag base massage system. The spring-loaded bag support arms gradually rise and keep the bag tensioned during emptying to ensure complete discharge of the resin flakes.
The arms also stop the bag from spouting or liner from sagging. According to Kuhn, this is a winning feature for Jowat. “What this does is assure material flows as the bag gets lighter by raising it so it’s easy to empty,” he said. The bag spout closure bar controls the flow of resins and pinches the neck of the bag above the point where the outlet spout is untied and re-tied. Once the spout is untied, the pinch bars are opened to allow discharge.
The pinch bars are interlocked and can only open after the access door in the dust cabinet has been closed. This is both for safety and for greater dust containment. An adjustable bag base massage system assures a consistent flow of the resins from any bags that have become compacted during transportation or storage. “With the Type 2 Discharger, our environmental quality and productivity have been enhanced,” confirms Mike Kuhn. “We are completely satisfied with the system.”
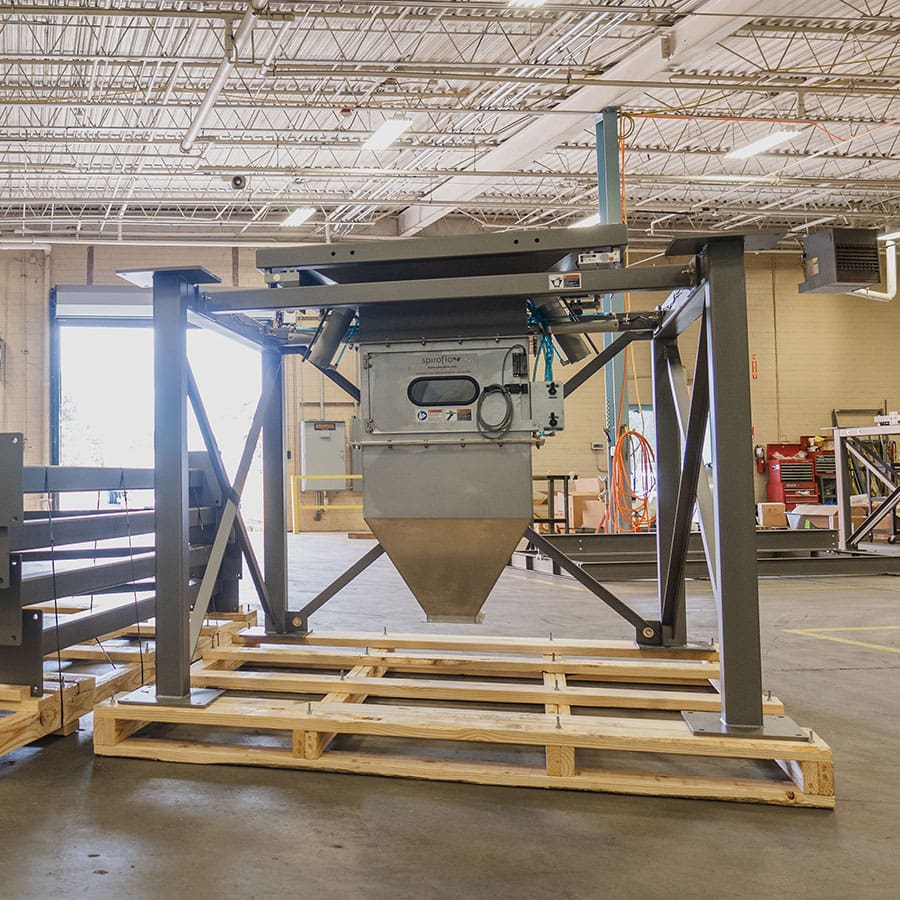
Jowat Adhesives – An Eco-Friendly Manufacturer With a Long Tradition
An eco-friendly manufacturer, Jowat Adhesives produces environmentally safe industrial adhesives for a variety of applications in the wood, furniture, paper, packaging, construction, upholstery, automotive, textile, general assembly, mattress, and foam converting industries. The industrial adhesives manufactured at the Jowat plant include dispersion, hot melt, solvent-based, moisture-curing, and a variety of others.
Jowat Corp. is a wholly owned subsidiary of Jowat Adhesives AG, a 90-year-old German company with sales in more than 60 countries. Jowat Corp. was formed in the USA in 1979 and ships adhesives worldwide from its High Point facility. For more details about the company, be sure to visit their website.
If You Want to Improve Your Production Process Like Jowat Did, Reach Out to Spiroflow – We’ll Be Happy to Help
Are you looking to enhance your production process with innovative conveyor solutions? Just like Jowat Adhesives, you can rely on Spiroflow’s expertise to tackle your manufacturing challenges. At Spiroflow, our team of the best industrial conveyor systems manufacturers is dedicated to designing and implementing custom-made conveyor technologies that address your specific needs, ensuring improved efficiency, safety, and productivity.
Whether it’s a unique bulk bag discharger or a comprehensive material handling system like a flexible screw conveyor, Spiroflow is ready to deliver. Contact us and discover how our tailored solutions can transform your production process. Let’s work together to achieve your operational goals and drive your business forward!
FAQ
What Is a Bulk Bag Discharger and How Does It Work?
A bulk bag discharger, such as the one custom-designed by Spiroflow for Jowat Adhesives, is an equipment piece used for unloading bulk bags filled with materials, in this case, resin flakes. It facilitates the controlled, dust-free transfer of material from large bags into a production system. Spiroflow’s model includes features like spring-loaded arms to maintain tension on the bag for complete emptying, a dust containment system for environmental safety, and an adjustable bag base massage system to ensure consistent material flow.
Why Did Jowat Adhesives Choose Spiroflow for Their Bulk Bag Discharger?
Jowat Adhesives selected Spiroflow for their bulk bag discharger/sack tip station due to Spiroflow’s ability to provide a completely enclosed, dust-tight solution. This was crucial for Jowat to prevent dust contamination in the production of their industrial adhesives. Spiroflow’s custom-designed discharger met all of Jowat’s specific requirements, including the ability to handle different sizes of bulk bags and integrate seamlessly into their existing manufacturing process.
How Did Spiroflow’s Solution Benefit Jowat Adhesives?
Spiroflow’s custom-designed bulk bag discharger brought numerous benefits to Jowat Adhesives, including improved operational efficiency, enhanced environmental quality by minimizing dust contamination, and increased productivity. The solution was clean, operator-friendly, and compact and offered seamless integration with Jowat’s central dust collection system. It allowed for the continuous, flawless operation of the plant, reflecting Spiroflow’s commitment to addressing the unique needs of its clients.
Can Spiroflow’s Bulk Bag Dischargers Handle Different Types of Materials?
Yes, Spiroflow’s bulk bag dischargers are versatile and capable of handling a variety of materials. For Jowat Adhesives, the discharger was designed to accommodate resin flakes from 1,000 lb Supersacks, 500 lb Mini-Sacks, or 50 lb bags. This flexibility is a testament to Spiroflow’s ability to create conveyor solutions tailored to the specific needs of their clients, ensuring that the discharger fits perfectly within the existing production process and material types.
What Makes Spiroflow Stand Out as a Provider of Industrial Conveyor Systems?
Spiroflow stands out due to its commitment to custom-made, innovative conveyor technologies tailored to specific industrial needs. Our company’s expertise in designing and implementing systems that improve efficiency, safety, and productivity is well-demonstrated in the success story with Jowat Adhesives. Spiroflow’s ability to understand and meet the unique challenges of its clients, combined with its dedication to quality and safety, makes our company a preferred choice for businesses looking to upgrade or enhance their production processes.