Looking for effective ways to reduce dusting when discharging bulk bags? You’re in the right place. Dusting can be a significant issue in bulk material handling, leading to increased cleanup efforts, reduced product yield, and higher operational costs. This article explores practical strategies and solutions, including advanced conveyor belt systems and bulk bag designs, to minimize dust release and improve efficiency in your operations.
Understanding the Dusting Dilemma in Bulk Bag Discharge
Unfortunately, dusting is a common problem in an industry like this. While bulk bags can be the most economical package for shipping semi-bulk quantities of dry bulk solids, they often get a bad rap from end-users. It’s because the process of unloading them can be dusty.
Excessive dusting during discharge obviously causes a mess requiring additional clean-up labor. However, it can cause significant profit reduction because every pound of product that lands on the floor reduces ingredient yield and increases input costs.
Dusting Can Be Quite Costly
We know of a food manufacturer whose bulk bag discharging stations create a lot of dusting during unloading. A plant visit confirmed the mess made during bulk bag discharging, but curiously their floors are always spotless! The plant has hose bibs everywhere, which encourages cleaning. Seemingly a good thing.
However, a thorough analysis of their ingredient yield showed that they were losing approximately $300,000.00 annually due to poor yield. Tons of products – along with a good chunk of profit – were being washed down the drain!
While it’s true that not all of that waste was directly attributable to dusting from bulk bag dischargers, most of it was. So, not only is dusting during bulk bag unloading a nuisance and housekeeping issue, but it can quickly affect – negatively – the bottom line.
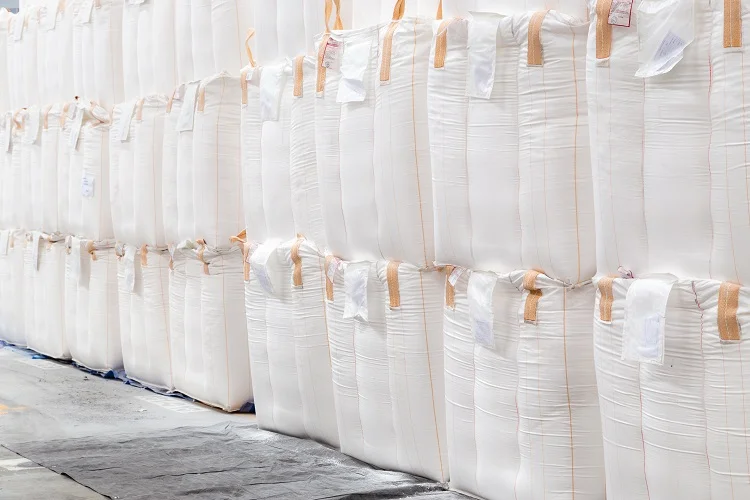
What Can Be Done – Ways to Reduce Dusting When Discharging Bulk Bags
Addressing the dusting issue during the discharge of bulk bags is crucial for maintaining a clean work environment and optimizing operational efficiency. From refining operator training to selecting the right bulk bag design and integrating advanced discharging equipment, we outline effective ways to reduce dusting when discharging bulk bags, ensuring a cleaner, more productive, and cost-effective operation.
Training
The biggest issue we see with bulk bag dischargers is that operators are not following the manufacturer’s operating instructions. Regardless of the equipment used to unload bulk bags, if it is not used properly, optimal dust containment cannot be achieved. Left to their own devices, operators will quickly figure out the easiest way to get the product out of the bag – and that often leads to unnecessary dust emissions.
Easy operation sounds like a good thing, but the reality of discharging bulk bags is that they require some effort to use properly. Work with your bulk bag discharger vendor to fully understand how their equipment should be used to the best effect, and then train and supervise your operators accordingly.
Bulk Bag Design
We often see situations where fine products sift through the fabric of bulk bags. If that sounds familiar your ingredient vendor should be willing to work with you to provide a bulk bag that eliminates this problem. The easiest solution is to use coated bulk bags that feature a film of polypropylene bonded to the inner surface of the bag fabric. This should cure most shifting problems. However, if a coated bag isn’t enough your vendor should be using a separate polyethylene liner.
Bulk Bag Discharging Equipment
Bulk bag dischargers come in many configurations. Some are better than others when it comes to dust containment. Look for designs that allow easy and safe access to the bag outlet spout while keeping it enclosed in a hopper that can be connected to a vacuum dust collection system. However, not all of these designs are created equal!
If the hopper that is under negative pressure is filled with the product during discharging, dusting will still be a problem. It’s when the hopper door is opened, and the product that has adhered to the inside of the door drops on the floor.
Ideally, the outlet spout of the bulk bag should protrude out of the hopper during discharge, so the only time the hopper sees dust is during the initial stage of product flow and perhaps at the end of the discharge cycle. Ergonomics are also a key criteria when selecting a bulk bag discharger.
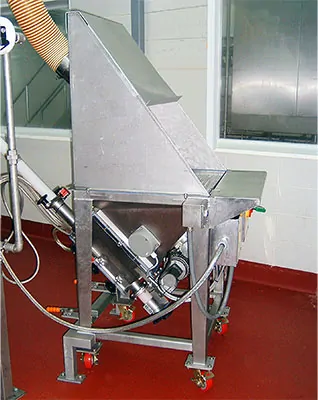
Streamlining Operations and Enhancing Dust Control With Spiroflow
As mentioned above, you don’t want your operators circumventing Standard Operating Procedures and creating excessive dusting because the bulk bag discharger is too difficult to use properly. Carefully evaluate dust containment features and ergonomic design when selecting a bulk bag discharger. Contact us at Spiroflow and get all the needed information for boosting your production. We’re one of the conveyor systems manufacturers that cherish the customers’ needs and requirements.