Customer Requirements
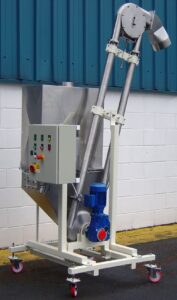
By maintaining the rope and disk assembly at a constant high speed, the conveyor produces an air stream that fluidizes and conveys product to the mixing vessel where the powder is centrifugally ejected.
This method of conveying allows varied production capacities from high to low, with low energy requirements and minimal production degradation and separation.
Soliant, LLC., a paint film manufacturer, needed a better way to weigh and mix 275 lb./ 125kg drums of acrylic resin.
Before purchasing a Spiroflow Aero Mechanical Conveyor (AMC), employees manually pushed 275 lb./ 125kg drums filled with powder to a scale for weighing and adding to a mix. Once weighed out, two employees manually scooped 1.5 lb/ 680g of powder at a time from the drums to the mixing vessel – the beginning stage of the Fluorex™ process.
Before scooping into the mixing vessel, employees first had to hand inspect and physically break up any lumps or sticky powder. Each application required an average of 25 minutes per employee or almost one man-hour hour for each operation.
Spiroflow Solution
Designed and custom built for Soliant, the all stainless steel conveyor and distribution system consists of an inclined 90”/ 2.3m long straight-line Aero Mechanical Conveyor with a sack tip hopper at the inlet.
- The Spiroflow AMC system is mounted on a mobile frame complete with two fixed and two swivel casters.
- When required to add material to the mixer, the mobile conveyor is positioned onto a 4’ x 4’/ 1.2 x 1.2m weigh platform that is sunk into the floor so that it’s top is flush with the factory floor.
- The weight of the conveyor is tared so that the precise amount of acrylic powder can be loaded into the conveyor feed hopper.
- The powder is tipped into the hopper through a plastic strip curtain located at the front of the dust hood above it. (The dust hood is connected to a dust extraction system that assures an environmentally safe dust free operation)
- A grid across the top of the hopper is used to break up any agglomerates of material, a main concern with the previous procedure.
- A rotary valve controls the flow rate from the hopper to the conveyor.
- Six air-operated vibratory pads strategically placed around the hopper ensure a consistent flow of powder into the rotary valve at the hopper outlet without bridging.
The conveyor has 3”/ 75mm conveying tubes and operates at a 45° angle. An air motor powers both the conveyor and rotary valve which is common in hazardous environments. An interlocked access panel facilitates cleaning of the internal conveyor components and a vision panel in one of the conveying tubes enables operators to determine when cleaning is required.